For many, Spring cleaning means washing windows, scrubbing floors, and doing some extra dusting and vacuuming. If you’re a facility operator or maintenance professional, your Spring to do list is quite a bit more extensive. There are a lot of responsibilities that need to be addressed every Spring, especially in climates that transition from cold weather to warm weather.
For the parts of the country that welcome warmer weather in the Spring, this is the time when facilities start preparing their cooling towers and chillers for cooling season. Any major repair and maintenance work should be completed, or at least be in progress, by this point. This includes chiller tube cleaning and inspections and general repairs for the cooling towers and condenser piping.
For cooling towers, it’s first important to ensure you’re in compliance with local regulations, if they apply. For example, any cooling towers in New York City that fall under the purview of Local Law 77 must be registered and updates to the Maintenance Program and Plan (MPP) should be under way.
Additionally, before you are ready to embark on cooling season, a final check on the state of your cooling water treatment systems is also in order. You don’t want to experience untimely issues that you’d have to correct while your plant is firing full-blast in the dog days of summer.
Here are some checks to ensure safe and efficient operation of your cooling water treatment program.
IMPORTANT: Never attempt to fix a mechanical or chemical issue unless you are trained and certified to do so. Safety should always come first. Consult a specialist before starting any mechanical or chemical related projects if you are not trained and certified to perform the work.
Cooling Tower Cleaning and Disinfection
Below is the statement issued by OSHA on recommended cooling tower cleaning maintenance:
“Preventing Legionella growth through cleaning will reduce the likelihood for exposure. Considerations for cleaning water systems in the workplace include:
- Cleaning and disinfecting cooling towers at least twice a year. Normally, this maintenance is performed before initial start-up when the cooling season begins and after shut-down in the fall.”
–OSHA Website – Legionellosis (Legionnaires’ Disease and Pontiac Fever)
The best way to ensure your cooling water treatment is effective for the season is to have it thoroughly cleaned and disinfected right before start-up. This includes the tower basin, fill, distribution deck and exterior surfaces. Even if you cleaned at the end of the Fall season, all the debris that collected over the winter months must be removed and any potential biological fouling that may have occurred must be eradicated before you fill the towers up for the season.
Inspect and Examine Chemical Feed Lines and Injection Points
If you see your chemical feed lines begin to experience calcification of chemistry at the injection points, now is a good time to remove, clean, and replace the tubing and injection fittings. In addition to the performance issues associated with leaking fittings and the waste of chemical, this is also a major safety issue for the personnel working around this equipment. This is highly concentrated residue from your chemical feed that, if dislodged and contacts skin or eyes, can cause serious damage. This is especially common with oxidizing biocides such as chlorine and bromine.
You do not want to interrupt chemical feed while the boiler is in operation to make these repairs, so do a visual inspection of all the chemical feed lines and stations before they go online. Correct any situation where you find this occurring right away.
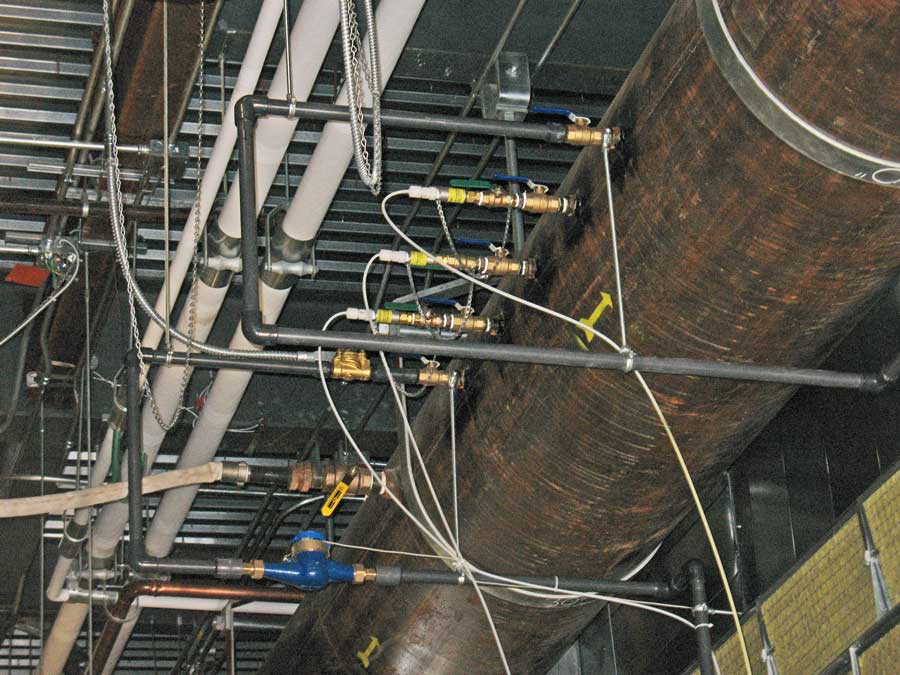
Check Water Source Quality
You set your cycles of concentration for cooling water scale and inhibitor chemistry and your blowdown based on certain characteristics of your facility’s incoming water supply, including TDS, pH, Hardness and Alkalinity. Prior to cooling season, it is a good idea to check these parameters to see if any have changed dramatically, which will impact both the cycles (the amount of times we can reuse the water in the tower) and the inhibitor chemistry you are running to keep solids in solution while minimizing corrosivity potential. For example, we often see changes to the water supply characteristics where well water is used and the well is changed during the offseason. It is a good idea to do an annual lab test of your incoming water source so you can track variances in quality.
Clean and Calibrate Monitoring Probes and Valves
Proper cooling water treatment programs utilize several probes to ensure accurate monitoring and control of the chemical treatment within the condenser water system. At a MINIMUM, this includes conductivity and flow, and can also include pH, ORP and PTSA. Prior to start-up, remove these probes to perform a thorough cleaning and calibration to ensure proper performance down the road when it is needed the most. Cooling water pH and ORP probes usually have an 18-month to 2-year life, so it may be a good time to replace them if you cannot hold the calibration.
It is also important to test and, if need be, open up your tower blowdown valve to ensure that no debris will prevent if from operating properly. A surefire way to have your tower go from clean to dirty over a hot weekend is not having the high TDS water purged automatically due to a clogged blowdown valve.
For those who are using more advanced remote monitoring controllers, software updates happen frequently and should be performed to ensure proper operation of the “brains” of your chemical feed and control technology.
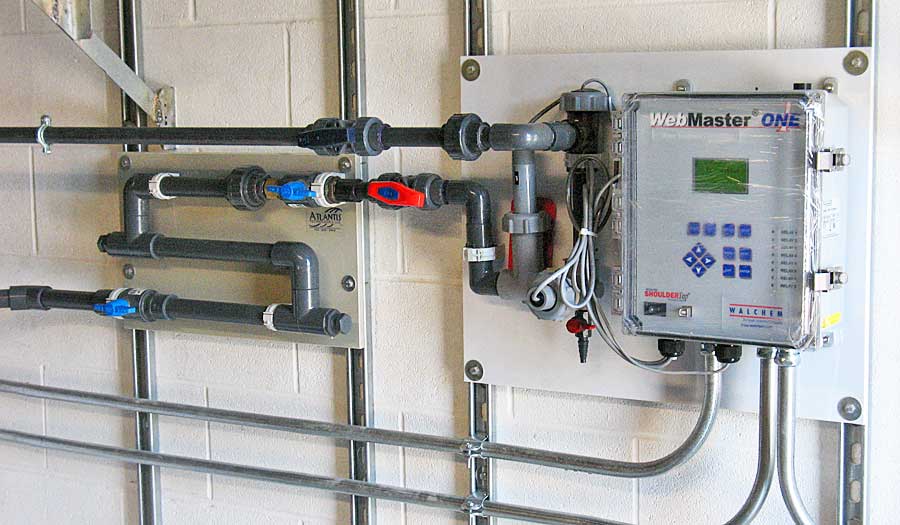
Review Testing Procedures and Examine Test Kits and Reagents
A big key to any successful cooling water treatment program is regular testing by the on-site personnel. And, the testing is only as good as the operators performing the tests and the equipment they are using to test the water. It may be a good idea for your onsite operators to have a refresher from your water treatment provider on the basics of the water treatment program, including how to test for the key parameters and what to do in case chemistry goes out of range.
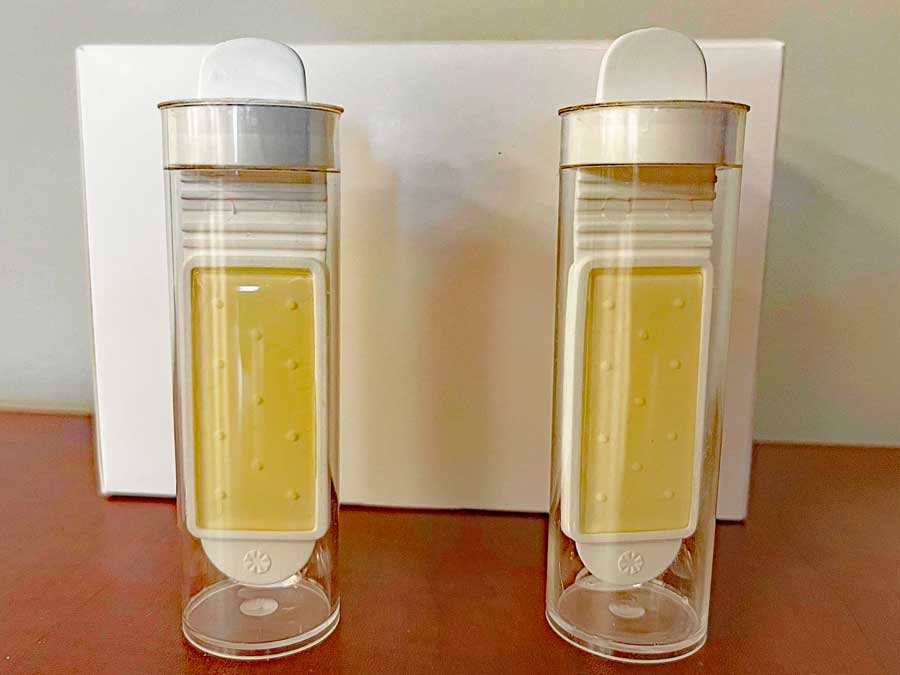
Also, now is the opportunity to calibrate your conductivity and pH testers and to check the expiration dates for the reagents being used to ensure they have not expired. For accounts that test microbio growth onsite via aerobic dipslide cultures, ordering a fresh supply is essential since these tests only have a 6-month shelf-life and whatever you have on-site is likely near or already past expiration.
Inspect Existing Chemical Inventory
Much like testing reagents, your chemical products also have a shelf life. Over time and with exposure to temperature, the delicate chemistry in your corrosion and scale inhibitors and biocides can result in coagulated residue at the bottom of your chemical containers, rendering the chemistry less effective. If you have containment tanks that house your chemical products, inspect the bottom of the tanks to ensure they have not collected months or years of old chemical residue that can impact the performance of the replenished chemistry. If necessary, a tank cleaning may be in order.
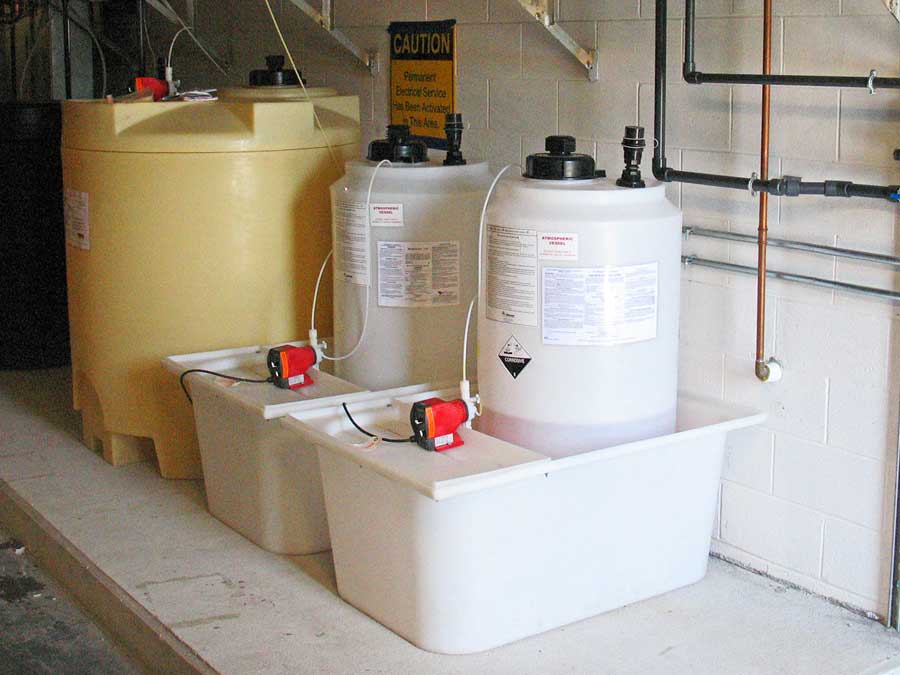
These are just some “last minute checks” for your water treatment prior to start-up to ensure smoother operation during the warm weather.
Clarity Has the Solution:
Proper water treatment, along with regular inspections and maintenance, can ensure your entire cooling system operates efficiently. Additionally, it will reduce unplanned downtime and maintenance costs and will extend the life of your equipment.
Clarity Water Technology has extensive experience with cooling systems. If you have any water treatment questions or issues as you get your towers ready for the season, just contact our team of water treatment experts.
If you’re in need of water treatment services, Clarity offers our proprietary technology, EcoSAFE, a cutting-edge solid feed water treatment for cooling towers that is more effective, economical and eco-friendly than traditional chemical solutions. A water treatment plan that incorporates EcoSAFE will protect your system and have your tower running at peak performance. We’ll be happy to conduct a FREE evaluation of your cooling system to see how a custom water treatment plan for your facility can save you money!